The following story is the second in a series produced in collaboration with KAXE/KBXE, an independent, nonprofit community radio station that tells the stories of northern Minnesota.
Minnesota taconite mine operator Cleveland-Cliffs is testing a new method for treating industrial wastewater in hopes of decreasing water, chemical and energy use — as well as costs.
The project is among several efforts by the company to lower its energy use as steelmakers face growing pressure from governments, investors, and customers to reduce the climate impact of their operations.
Energy efficiency is often the quickest and most cost-effective way for companies to cut their carbon footprint. When it comes to mining, the opportunity is as large as the massive trucks and other heavy-duty equipment used to haul and process taconite.
Cleveland-Cliffs was recently recognized by the U.S. Department of Energy for cutting companywide energy use by nearly one-third since 2017. The federal agency’s office of industrial efficiency and decarbonization is monitoring the water treatment project, as well.
“Bringing these emerging technologies out of the laboratory and onto the factory floor is a critical part of reaching our industrial decarbonization goals,” said Avi Schultz, director of the Industrial Efficiency and Decarbonization Office.
Decarbonization refers to the process of lowering or eliminating emissions of carbon dioxide, the heat-trapping greenhouse gas that causes climate change. The steel industry is among the three biggest sources of carbon emissions on the planet, accounting for around 8% of all global carbon emissions. Most steelmakers, including those that own and operate the Iron Range’s taconite mines, have adopted internal goals for reducing emissions.
“One of the most important issues impacting our industry, our stakeholders and our planet is climate change,” Cleveland-Cliffs told its investors this year. “We plan to achieve our GHG emissions reduction goal by focusing on actionable, commercially viable technologies and solutions while supporting research for breakthrough technologies for the primary iron and steel sector.”
It cited its partnership with the U.S. Department of Energy to implement and test energy-saving technology as a key piece of its climate strategy.
Cleveland-Cliffs operates Hibbing Taconite, United Taconite, Northshore Mining and the Minorca Mine on Minnesota’s Iron Range. The company is working with Arizona-based Dynamic Water Technologies on two pilot projects to reduce lost water and energy waste from treating wastewater.
The technologies are first being tested in a Cleveland, Ohio, plant.
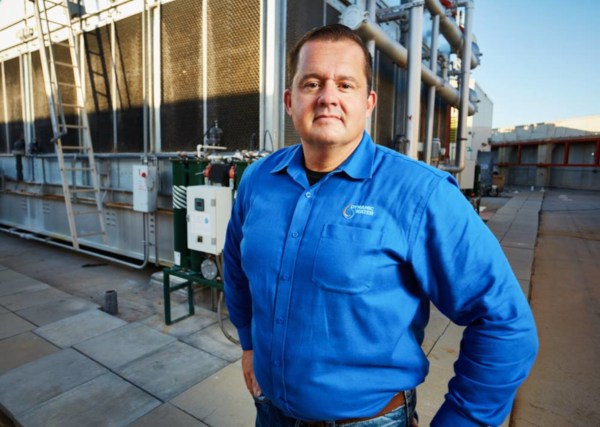
Michael Boyko is the co-founder and director of business development for Dynamic Water Technologies. He said the equipment being studied is fundamentally better at what it does.
“These technologies are justified because they do it better, faster, and more cost effectively,” Boyko said. “If they were just an environmental benefit with no water, sewer, or chemical savings, it would be a harder sell to industrial clients.”
The project is piloting two different technologies for oil and hydrocarbon removal. One is called electrocoagulation, and the other is electrochemical water treatment.
Electrocoagulation is done by applying direct-current electricity to iron plates, which creates a coagulant that bonds with contaminants in the water and makes them much larger. These enlarged particles then either float to the top or sink to the bottom, making them easier to remove.
Boyko said this process eliminates the need for several chemical processes and various agitators, mixers and pumps along the way, making it more cost-effective and faster.
“There’s definitely a lot of energy savings, because we’re doing in one process what seven different chemical water treatment systems basically were doing,” he said.
Electrochemical water treatment, meanwhile, replaces chemical treatment of processed water within cooling towers using dynamic scale reactor technology. This technology quickens the natural process of scale buildup from minerals within reactor chambers, sequestering it for later removal. The process allows the same water to cycle through the system eight or more times, instead of as few as three.
Cleveland-Cliffs did not respond to interview requests, but the company touted the technology’s environmental benefits in its most recent sustainability report.
“The alternative technology yielded significant reduction in solid waste from process water, and preliminary data shows it could also increase process water reuse,” the report said.
This technology is already in use at Los Angeles City Hall and the Juliette Gordon Low Federal Building in Savannah, Georgia, with federal government testing validating the positive effects.
Cleveland-Cliffs also participates in the Department of Energy’s Better Buildings program. The voluntary program encourages improved energy performance across industrial operations, which account for more than one-third of total U.S. end-use energy consumption.
“This is essential for the industrial sector, as inattention to greenhouse gas emissions, inefficient energy and water use, and excessive waste production can hurt domestic competitiveness in a global marketplace,” the department says.
A detailed report of the Cleveland-Cliffs project is expected to be issued by the end of the year.