Mercedes-Benz developers are already working on automotive progress “far beyond the current period of transformation,” the company explains. While the Vision EQXX technology platform provides a glimpse of the near future, the car manufacturer’s experts are already working on a new generation of innovations.
Brakes in the electric motor-transmission unit
One strand of research is focused on the brakes, which the German carmaker wants to make as aerodynamic and low-maintenance as possible. To this end, they are moving the brakes from their position inside the wheels to an integrated electric drive unit at the front or rear axle, where they take up very little installation space. The car manufacturer is pursuing this approach “as electric vehicles brake primarily through recuperation,” which opens up new avenues in the development of mechanical brakes.
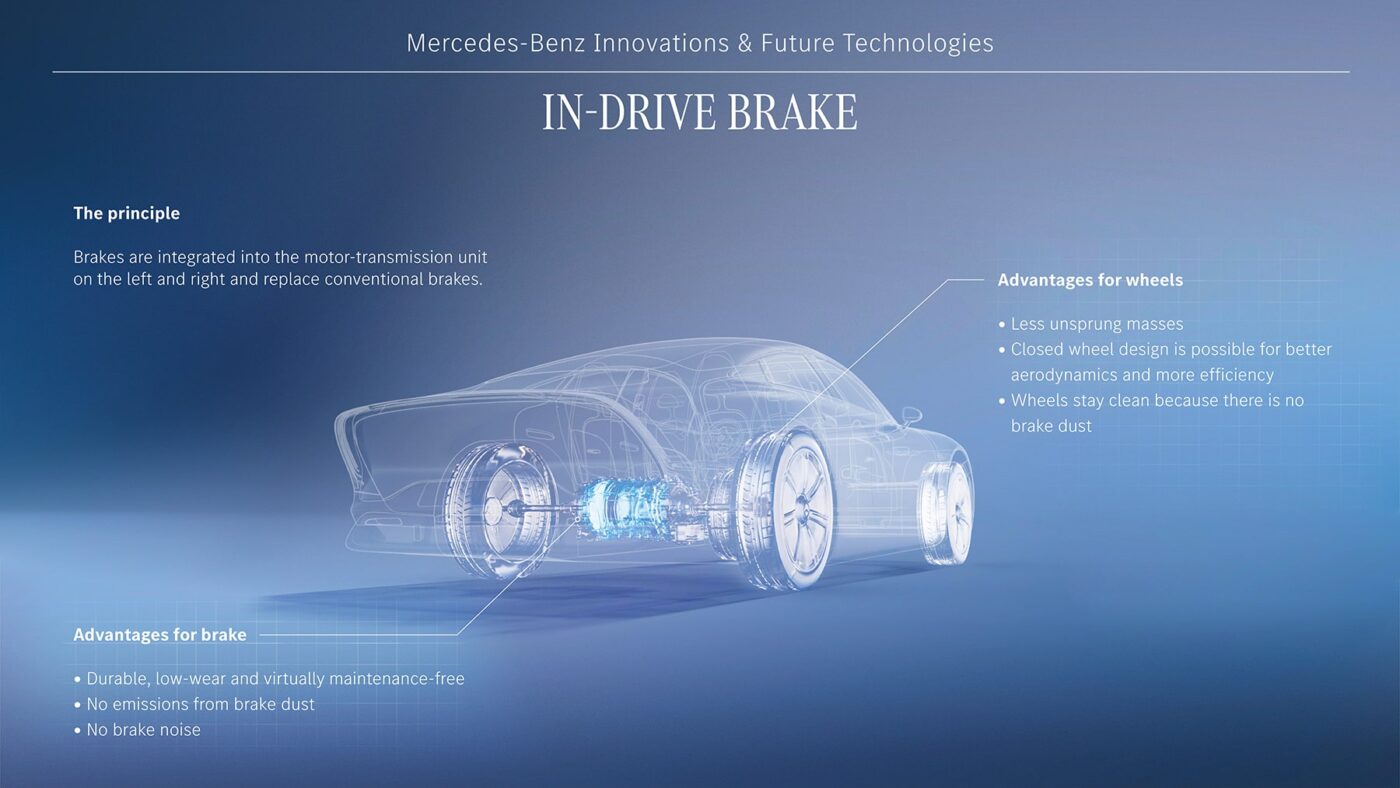
Centralised in this way, the in-drive brake should, according to current research results, hardly wear out, not rust and be virtually maintenance-free. In addition, the braking effect can be well controlled. “This would make it very durable and reliable,” summarises Mercedes-Benz. “In addition, there would be no particulate emissions into the atmosphere. Braking noise and brake cleaning could also become a thing of the past.”
The design should also allow for a significantly lighter wheel/tyre combination and thus less unsprung mass, which in turn benefits ride comfort. The developers note that completely closed rims for improved aerodynamics would also be possible, as openings for brake cooling would no longer be necessary.
Micro-converter directly at battery cell level
Another promising innovation mentioned is a power converter as a central player in the high-voltage architecture of future electric cars. It is intended to increase the battery’s efficiency through control processes at the cell level. Mercedes-Benz explains: “In future, a programmable micro-converter could go beyond the limits of current electrical inverter systems and revolutionise existing high-voltage architectures. The basis for this is the integration of these micro-converters directly at battery-cell level, which could enable individual control of battery-cell pairs as well as communication between cells.”
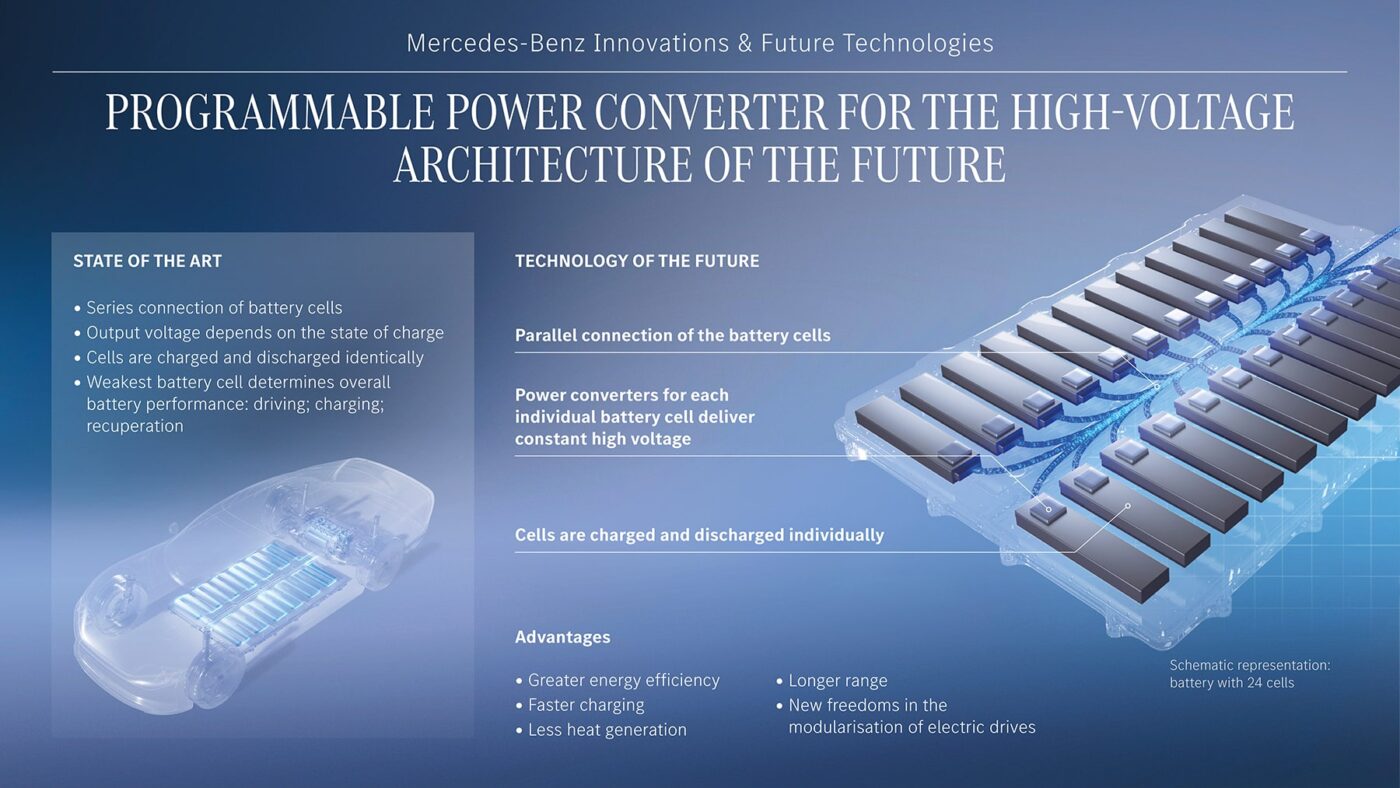
In practice, a power converter consisting of several micro-converters will be connected directly to any number of battery cells. The approach makes it possible to control cells individually and regulate the output voltage level of this unit. “Current research results show it is possible to provide a constant HV output of 800 volts, regardless of the state of charge (SoC) and the state of health (SoH) of the individual cells,” Mercedes says. The output voltage of this vehicle battery is no longer dependent on the number of battery cells connected in series. The number is only determined by the desired performance and capacity class. The developers believe this technological approach could also increase the range and optimise the energy flow for bidirectional charging processes.
A side effect could also be new freedoms in modularising electric drives. That is because: “The programmable micro-converters could reduce the production variants of electrical components and could also be easily reprogrammed for the latest updates. As standardised parts, they could thus lower the use of resources. They have the potential for use in many future Mercedes-Benz electric models,” the company explains.
To summarise, the new technology has the potential to integrate several power electronics functions into the battery. According to Mercedes-Benz, this means that various power components could be realised by the battery itself, and a new level of high integration in electric vehicles could be achieved.
Solar paint on all exterior surfaces of the vehicle
The car manufacturer is also researching a solar paint that “could generate enough electricity for more than 12,000 km per year.” It consists of innovative solar modules that are five micrometres wide (“significantly thinner than a human hair”) and weigh just 50 grams per square metre. The modules are applied like a wafer-thin paste.
“The solar cells have a high efficiency of 20 per cent. An area of 11 square metres (equivalent to the surface of a mid-size SUV) could produce energy for up to 12,000 kilometres a year under ideal conditions,” says the company. The energy generated by the solar cells is then used for driving or fed directly into the high-voltage battery. Moreover, the photovoltaic system also generates energy when the vehicle is switched off. It could thus “be a highly effective solution for increased electric range and fewer charging stops.”
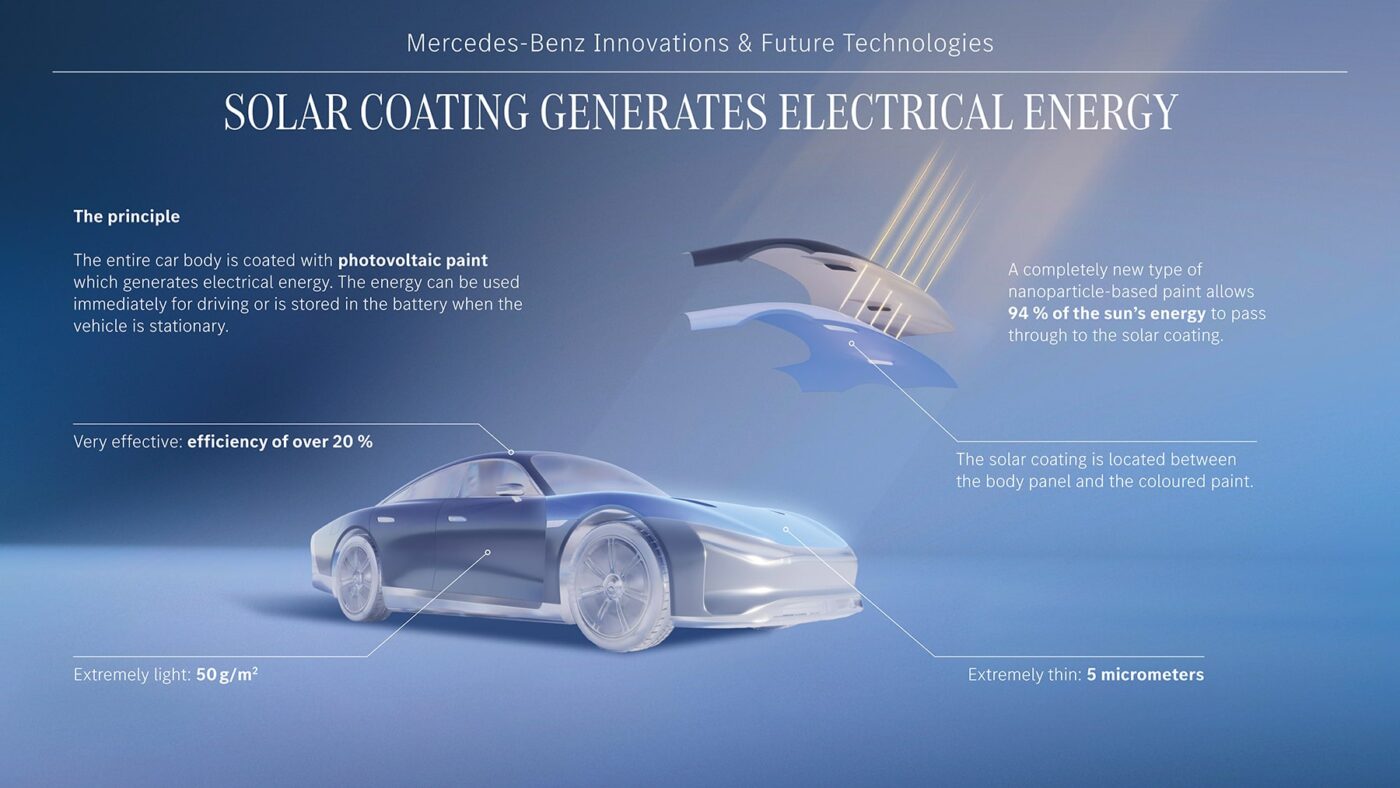
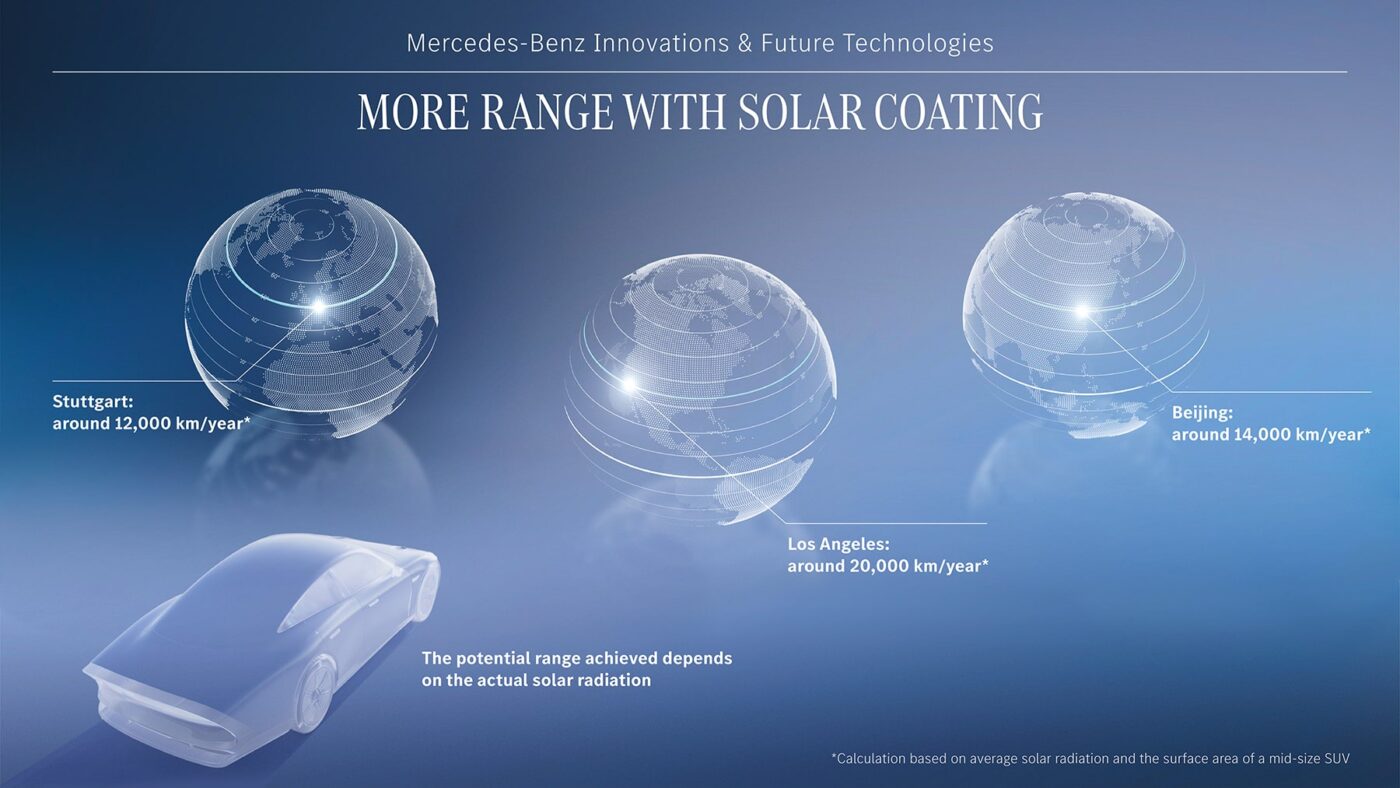
In practice, the yield naturally depends on shading, sun intensity and geographical location. Mercedes gives two examples: “Statistically, Mercedes-Benz drivers in Stuttgart, Germany, cover an average of 52 kilometres a day. Around 62 per cent of this distance would be covered using solar energy. In Los Angeles, there is even a surplus of energy from solar radiation. The customer could cover 100 per cent of their driving distance on average by solar energy. The surplus achieved could be fed directly into the home network via bidirectional charging.”
According to the developers, the solar paint is said to have a high level of efficiency and be free of rare earths and silicon. It can be easily recycled and is considerably cheaper to manufacture than conventional solar modules. According to Mercedes-Benz, the research department is currently working intensively on making it possible to use the new type of solar paint on all exterior surfaces of the vehicle – regardless of their shape and angle of inclination.